
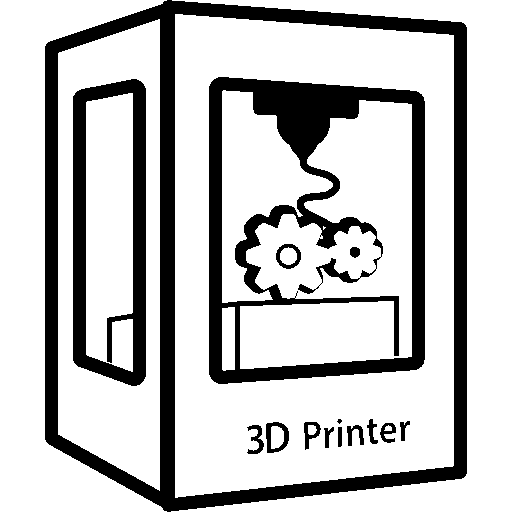
Yeah, makes sense based on where the sensor is, my heater didn’t have a thermocouple on it so I drilled a hole for a thermistor midplate, it’s super slow to respond is the downside but in theory it should be accurate enough.
I don’t have experience with the bambu, in theory everything will experience thermal expansion but for the voron setup, the bimetallic construction is some of the issue, they have different thermal expansion properties so it can cause deflections. Part quality will vary wildly depending on sourcing too, vorons are very diy and open as the draw, but there’s just so much variability from sourcing, mods, assembly etc.
You can muffle the beeper pretty effectively with some tape, the old air fryer we had terrified one of the dogs because of the incessant beeping. My coffee scale by default beeps whenever you touch it, thankfully that’s 100% mutable.
I also hate this.