
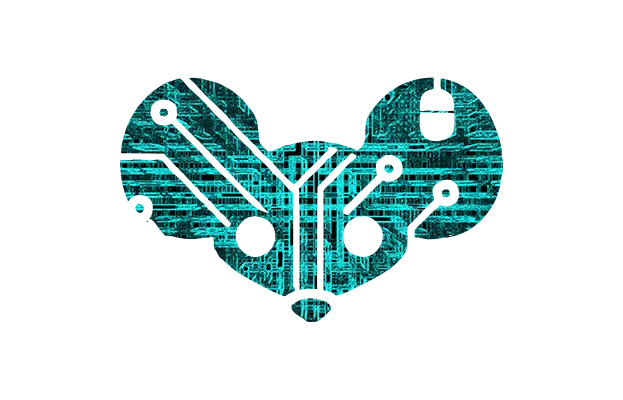
It’s supposed to be in the US also.
It’s supposed to be in the US also.
There is a lot of potential here. I have little doubt the printer and slicer algorithm will make it’s way to mainstream printing at some point.
And the left is often paralyzed by the “complexity” of a solution and offers little no refuge for those in need. Sadly making those half baked ignorant simple solutions the only thing offered.
Yeah, Orca has issues with Fedora. The appImages often fail in particular. But I do have it running on Fedora Cinnamon 42 and Aurora 42, (spin off of Kinninite 42) with the flatpack from the GitHub.
I recommend installing the open light and open dark theme for a better user experience in FreeCAD. Everything seems a bit clear and easier to use, YMMV
As a house with 3 dogs and 2 cats, it’s not a real problem. Sometime a quick wipe is needed, but the critters ain’t going to interfere with any printing.
When you slice the keychain, have you painted in the letters with the chosen colors? Does it show the purge tower after slicing? And when you click to send it to the printer, does the popup screen show 2 spool images and colors? If it does, then the text is there and just embedded below the surface. and you need to raise it up to be flush with the surface.
Bambu Studio is ass for embedding text and some others things as well. Orca Slicer and Prusa Slicer a lot better with adding text.
Yeah, it could be possible to only ever need the mini and 80% is perhaps conservative. But, I as much as I find my Bambu Mini can cover the majority of my printing needs these days, I still need the print volume my Prusa Mk3s has for a very good number of practical prints I design and print. The real world often demands real world size and hates pieced together part designs lack of strength. And I still often need to resort to my metal working shop with lathe, mill, drill press and welders to make serious parts because plastic just ain’t it.
If it works, it’s a superb deal. And the print area will probably cover 80% of everything you might ever print.
Edit: Print quality is more about your ability to tune your printer, no matter the brand, then it is about the printer brand itself.
You are not alone! I have always been able to do that too. It still doesn’t help with the tinnitus I’ve had since I was 4 or 5 though.
What was a revelation to me was the idea that everyone was only sleeping 3 or 4 hours a night. I thought I was perfectly normal in not sleeping for normal time spans. And despite the drugs and cpap machine I’m prescribed, I still can only sleep 5 or 6 hours now and often less. But I often am able to get to REM sleep now.
This is kind of what I know from my experience. I have an A1 Mini with AMS lite and my trusty 5 year old Prusa Mk3s running Klipper. Not exactly the same, but close.
Mechanically, the linear rails vs the linear rods are more rigid and lead better overall printer rigidity than the more flexible linear rods. Is it enough to matter? With input shaping easily available on both printers, not really. But, those rails will require a bit more maintenance than the rods. My mini regularly prompts for cleaning and re-lubricating every so many hours of run time. Is it hard? Nope, but it IS something Bambu really recommends. The linear rod bearings are supposed to be greased before installation, (whether Soval does this or not is a question. Prusa didn’t bother with my kit), And because the rod bearings have wiper seals to keep the dust out and the grease in, a quick wipe with a clean dry paper towel is all that’s needed. No exterior lubrication required.
The AMS Lite is kind of nice, it keeps 4 spools of filament ready to go. And I keep 4 different colors ready or a spool to run out and then take advantage of being able to easily swap to another spool mid print and keep printing. I have done just enough multi-color prints to say I know how. Mostly just signage though. And it’s very wasteful as a rule. The RFID tags identification and setup isn’t worth the extra cost I need to pay vs the “generic” filaments I buy. I am not so unskilled or lazy to set up my own profiles quickly and easily. And the few spools of Bambu filament I have used has demonstrated it’s no better than any of the small handful cheaper brands I normally use. This is a YMMV situation. The Soval does not offer a builtin solution for the AMS, but some few more universal 3rd party units are now starting to come on the market.
Another “this may or may not matter to you” is that Bambu runs on legacy Marlin and the Soval runs on Klipper. Adding things to Bambu’s version of Marlin while doable, is a pain in the butt. Not much information is available on their version. For example, I wanted to turn off the input shaping at the start of every print. It’s noisy and not needed for every print. It took me a couple of weeks to find and learn to edit the intro macro to achieve my goal. Klipper is far, far easier to edit and make changes in. And you can access things like Obico for Klipper to monitor prints for spaghetti detection-- which Bambu cannot do. You can also more easily ignore a region if a plate full of models has one model fail at some point. Bambu requires the Handy app and you need to be logged into Bambu to use it I think. Studio offers no such functionality on the desktop.
The TL;DR: Your choice depends on what YOU want from your printer. It’s a YMMV all the way down. I do not regret my purchase of the Mini, but I won’t ever be buying another Bambu. But that’s just me.
Infills over 10 to 15 percent get you very little increase in strength. It’s not until you get to the sweet spot of 80-85 percent infill rates do you get a real boost in strength. Then above about 85% the gains again taper off dramatically all the way to 100% infill. Otherwise you are merely wasting filament and money to just feel good. If you need more strength, add more perimeters and tops and bottoms.
I would use a .60mm nozzle, PETG or PLA will work just fine, 4 perimeters, and 4 top and bottom layers. And either 10% cubic or gyroid infill. That should create a part that will last for years.
I grew up a poor farm boy, so we never had a VCR when I was a kid. And they really weren’t a thing anyway when I was young. And according to my Father, us kids were the remote!
Did you ever peer into the back of the TV when a tube would burn out and your Dad would pull the cabinet out, then remove the back and try to see which tube didn’t light up when the set was powered up? It was a marvelous sight! It often took us a few days before we would get to town before we could stop into the local drug store that had a tube tester and had a selection of the common tubes to buy.
That’s what I love about mine. Automatic lid raise and lower as you walk in, heated ring and water, (both adjustable temp), air dry, (again heated), and charcoal filtered air filtration to minimize the stench from that drive through burrito.
It’s the posh life. Very nearly the equal to having your own chamberlain.
You need to use the power washer setting. Takes the paint right off the wall…
I was thinking of even older things.
The feel of the keys and staccato sounds of a mechanical typewriter.
The sound of a wringer/washer machine
The muffled sound of my am band 9 transistor pocket radio “hiding” under my pillow late at night for as long as the 9V battery would last (I loved the Mystery Radio Theater show that started at 10pm)
The soft crackling sound of a tube black and white TV as all the tubes warmed up. (And the time it took to do so)
The sound and smell of the percolator coffee pot in the morning
The sound of a wooden screen slamming shut
The smell and sound of a mimeograph machine printing copies in the school/church office (And the slight buzz you could get from copy fluid-- Petroleum aromatics Yum!)
Doing my math homework with a slide rule.
The smell of a fresh fired paper hull shotgun shell on a cold crisp late fall morning
And so much more that no longer exists.
A perfect zero. I have done all of those things and more that the creator of that list can’t even imagine. Things that were everyday common but have faded beyond memory, (and aren’t missed at all).
And there is little reason to do input shaping on the start of every print unless you change the mass of the moving parts by a noticeable amount. And even then, it does nothing once the print starts. You get what you get anyway when the print is finished.
What would be better is if a printer could measure and adapt to the changing resonances as the printer was printing. But I suspect that ain’t going to happen anytime soon due the complexity and the ultimate question: “How good does good enough really need to be.”
Only if the lock isn’t worn or dirty on the inside. I wouldn’t trust this for any outdoor lock or older lock. Even cheap locks with poor fit and finish causing rough operation would not be a good idea. This is a fun gimmick that could easily cost you more money than it’s worth.
The only way I might use it is if I were to use the 3D printed key as a pattern to cast a metal one. And I ain’t got time for that.
Like most prepper things for sale, this is a better product to skin money from the ignorant and the unreasonably fearful than it is truly useful. It assumes you have electricity and the functioning equipment to access it.
In a real prepper situation, you either already ready have the knowledge in your head, (the best method), or you have real books and pamphlets to read, (slow to access).
Remember Kiddies, if a real SHTF gets here, there not only won’t be no google or youtube, but there won’t be much time to use it anyway. Survival is a real time sink. And most living in the big cities will simply die in place anyway.